Rozpoczynam nowy watek, aby niniejszy instruktaż nie był „skażony” innymi informacjami, gdybym kontynuował to wątku ogólnym „Skala S powraca” oraz aby tytuł jednoznacznie informował o zawartości. Wątek jest umieszczony nadal w H0, proszę PT. Moderatorów o przeniesienie gdy tylko uda Wam się otworzyć wątek dla S lub ogólnie dla rzadziej spotykanych skal.
Budowa SM 03 zaczęła się w czasie świątecznym w 2016 roku. Nooo, to naprawdę już 5 lat? Hmmm… Postanowiłem powrócić do modelarstwa po wieloletniej przerwie. Pomimo, że w szafie nadal czekała na dokończenie EU 07 (i nadal czeka), chciałem zrobić coś od początku. Miałem wtedy też pewien plan makietowy, który raczej pozostanie w sferze zamierzeń, i do tego planu potrzebowałem manewrówki. Ale czegoś małego, nie stonki czy czegoś w tym stylu. Po wielu dniach myślenia na placu boju pozostały SM 30 i SM 03. SM 30 bo mi się bardzo podoba i SM 03 bo… mała, no i też mi się podoba. Jeszcze gdzieś tam w rezerwie była 401Da ale ta lokomotywa ma jakieś takie pokraczne (moim zdaniem) podwozie z tymi masami na osiach kół i nienaturalnie długimi zwisami na przód i tył… no, nie podoba mi się to, choć „od pasa w górę” lokomotywa ładna. Wygrała SM 03 bo nie ma wózków i niby będzie łatwiej. Potem żałowałem tej decyzji bo i tak włożyłem ogrom pracy w jej budowę, więc brak tych dwóch wózków niewiele mi czasu zaoszczędził – a co ja przeżyłem aby upakować dekoder, głośnik, kondensator w to maleńkie wnętrze SM 03, oczywiście przy pełnym odwzorowaniu kabiny, to tylko ja wiem, choć postaram się tu przeżycia te Kolegom pokazać i opisać.
To był krótki wstęp czyli dość ględzenia o niczym. Teraz będzie relacji
CZĘŚĆ PIERWSZA
Skoro decyzja o typie lokomotywy zapadła, poszukałem kół w moich gromadzonych przez lata zapasach modelarskich różności. Znalazłem takie jak na zdjęciu, nawet nie wiem od jakiego parowozu z H0, ważne że obręcz wymiarowo dobra.
Pozostawał temat szprych ale na to miałem metodę wymyśloną około 30 lat temu, na użytek budowy SP45. Metodę, która pozwala wymienić szprychy nie tracąc fabrycznego współosiowego położenia piasty osi/wału i obręczy oraz prostopadłości osi/wału i powierzchni czołowej koła. Jak? Otóż, rysuję na kartonie koła w skali modelu, wytyczam położenie szprych, następnie wycinam z kół wszystkie szprychy poza dwoma lub trzema, które zapewniają utrzymanie współosiowości. Tak przygotowane koła naklejam na karton bardzo dokładnie osiowo, wklejam w pusty obszar odpowiednią ilość nowych szprych zgodnie z liniami na rysunku. Po zaschnięciu kleju wycinam pozostałe „stare” szprychy i uzupełniam nowe oraz doklejam odciążek z PS zgodnie z wymiarami nowego koła. Koło jest gotowe. Opisałem tę metodę jako ogólną, a w tym przypadku miałem łatwiej, gdyż dwie szprychy (w tym jedna z gniazdem czopu korbowego) były na swoim miejscu. Zastosowany klej to CA a nowe szprychy to po prostu paski PS o właściwej grubości. Na zdjęciach widzicie proces a pełną metamorfozę pokazuje zdjęcie ostatnie.
Technikę wklejania szprych opisałem szczegółowo jeszcze w 2017 roku w wątku „startowym” – aby nie zmuszać Was do szukania, zacytuję odpowiedni fragment: „…trzeba mieć szprychę dociętą dokładnie tak aby w danym miejscu przeznaczenia wchodziła na lekki wcisk. Jak już ją mamy odpowiednio dociętą to wciskamy a następnie ustawiamy idealnie wzdłuż linii przebiegu wyznaczonym na rysunku. Następnie dajemy kropelkę kleju CA na paseczek 1mm odcięty z blaszki mosiężnej 0,1mm (sprawdzony sposób aby nie nabrać za dużo kleju) i przykładamy delikatnie w pobliże miejsca spoiny. Klej CA spływa między klejone elementy i natychmiast łączy elementy nie poruszając szprychy względem piasty lub obręczy (uwaga! klej musi być rzadki - czyli świeży). Następnie robimy to samo w drugiej spoinie, może być mniej delikatnie bo szprycha już się trzyma jak pieron - nie ruszy się na 100%. No i tak da capo z każda szprychą.
Jest wyjątek - miejsca gdzie trudno uzyskać pożądany wcisk i szprycha "lata". Wtedy trzeba ją wstępnie złapać absolutnie minimalną ilością kleju nitro, z jednej strony, potem ustawić spokojnie (mamy na to ok. minuty) i dalej jak wyżej z klejem CA.
Jeszcze jedno. W kołach, gdzie mamy duże wyoblenia między szprychami należy wypełnić te przestrzenie (umiarkowanie) distalem i okrągłym iglakiem ukształtować. W SM03 na szczęście takiej konieczności nie było bo oryginalnie koła te są dość kanciaste w środku, więc wystarczyło małe "nadlanie" CA i lekki szlif nierówności.”
Koniec cytatu, ten dokładny opis wydaje mi się pomocny, gdyby ktoś chciał przerabiać koła zamiast… kupić w sklepie!
Kolejny problem do rozwiązani to napęd. Początkowo chciałem wykonać go samodzielnie bo w SM 03 jest prosty, zacząłem już rysować i liczyć przełożenia w oparciu o moje zasoby kół zębatych (na zdjęciu).
Ale potem puknąłem się w czoło i przypomniałem sobie, że to nie lata 80-te, gdy o gotowych napędach można było pomarzyć (chyba, że ze złomu pikowskiego, którego zawsze pod Halą Targową było sporo) i w internetach znalazłem odpowiedni napęd, z jakiegoś germańskiego tramwaju H0, produkcji PMT. Rozstaw osi pasował idealnie…
…pozostał jednak montaż nowych kół, co nie było proste bo osie dla H0 są krótsze (a koło zębate trzeba było zachować) oraz średnica wału mniejsza niż otwór w kole. Dzięki zastosowaniu tulejki z rurki mosiężnej cel został osiągnięty. Aha, w międzyczasie koła zostały pomalowane a w ramię korby zostały zamontowane czopy wiązarów. Po zmontowaniu wyglądało to już całkiem dobrze, czyż nie?
KONIEC CZĘŚCI PIERWSZEJ
Budowa SM 03 zaczęła się w czasie świątecznym w 2016 roku. Nooo, to naprawdę już 5 lat? Hmmm… Postanowiłem powrócić do modelarstwa po wieloletniej przerwie. Pomimo, że w szafie nadal czekała na dokończenie EU 07 (i nadal czeka), chciałem zrobić coś od początku. Miałem wtedy też pewien plan makietowy, który raczej pozostanie w sferze zamierzeń, i do tego planu potrzebowałem manewrówki. Ale czegoś małego, nie stonki czy czegoś w tym stylu. Po wielu dniach myślenia na placu boju pozostały SM 30 i SM 03. SM 30 bo mi się bardzo podoba i SM 03 bo… mała, no i też mi się podoba. Jeszcze gdzieś tam w rezerwie była 401Da ale ta lokomotywa ma jakieś takie pokraczne (moim zdaniem) podwozie z tymi masami na osiach kół i nienaturalnie długimi zwisami na przód i tył… no, nie podoba mi się to, choć „od pasa w górę” lokomotywa ładna. Wygrała SM 03 bo nie ma wózków i niby będzie łatwiej. Potem żałowałem tej decyzji bo i tak włożyłem ogrom pracy w jej budowę, więc brak tych dwóch wózków niewiele mi czasu zaoszczędził – a co ja przeżyłem aby upakować dekoder, głośnik, kondensator w to maleńkie wnętrze SM 03, oczywiście przy pełnym odwzorowaniu kabiny, to tylko ja wiem, choć postaram się tu przeżycia te Kolegom pokazać i opisać.
To był krótki wstęp czyli dość ględzenia o niczym. Teraz będzie relacji
CZĘŚĆ PIERWSZA
Skoro decyzja o typie lokomotywy zapadła, poszukałem kół w moich gromadzonych przez lata zapasach modelarskich różności. Znalazłem takie jak na zdjęciu, nawet nie wiem od jakiego parowozu z H0, ważne że obręcz wymiarowo dobra.

Pozostawał temat szprych ale na to miałem metodę wymyśloną około 30 lat temu, na użytek budowy SP45. Metodę, która pozwala wymienić szprychy nie tracąc fabrycznego współosiowego położenia piasty osi/wału i obręczy oraz prostopadłości osi/wału i powierzchni czołowej koła. Jak? Otóż, rysuję na kartonie koła w skali modelu, wytyczam położenie szprych, następnie wycinam z kół wszystkie szprychy poza dwoma lub trzema, które zapewniają utrzymanie współosiowości. Tak przygotowane koła naklejam na karton bardzo dokładnie osiowo, wklejam w pusty obszar odpowiednią ilość nowych szprych zgodnie z liniami na rysunku. Po zaschnięciu kleju wycinam pozostałe „stare” szprychy i uzupełniam nowe oraz doklejam odciążek z PS zgodnie z wymiarami nowego koła. Koło jest gotowe. Opisałem tę metodę jako ogólną, a w tym przypadku miałem łatwiej, gdyż dwie szprychy (w tym jedna z gniazdem czopu korbowego) były na swoim miejscu. Zastosowany klej to CA a nowe szprychy to po prostu paski PS o właściwej grubości. Na zdjęciach widzicie proces a pełną metamorfozę pokazuje zdjęcie ostatnie.
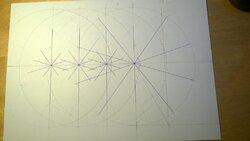
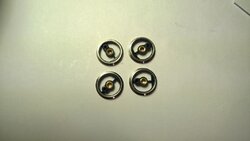
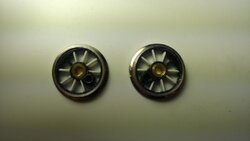
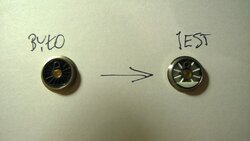
Technikę wklejania szprych opisałem szczegółowo jeszcze w 2017 roku w wątku „startowym” – aby nie zmuszać Was do szukania, zacytuję odpowiedni fragment: „…trzeba mieć szprychę dociętą dokładnie tak aby w danym miejscu przeznaczenia wchodziła na lekki wcisk. Jak już ją mamy odpowiednio dociętą to wciskamy a następnie ustawiamy idealnie wzdłuż linii przebiegu wyznaczonym na rysunku. Następnie dajemy kropelkę kleju CA na paseczek 1mm odcięty z blaszki mosiężnej 0,1mm (sprawdzony sposób aby nie nabrać za dużo kleju) i przykładamy delikatnie w pobliże miejsca spoiny. Klej CA spływa między klejone elementy i natychmiast łączy elementy nie poruszając szprychy względem piasty lub obręczy (uwaga! klej musi być rzadki - czyli świeży). Następnie robimy to samo w drugiej spoinie, może być mniej delikatnie bo szprycha już się trzyma jak pieron - nie ruszy się na 100%. No i tak da capo z każda szprychą.
Jest wyjątek - miejsca gdzie trudno uzyskać pożądany wcisk i szprycha "lata". Wtedy trzeba ją wstępnie złapać absolutnie minimalną ilością kleju nitro, z jednej strony, potem ustawić spokojnie (mamy na to ok. minuty) i dalej jak wyżej z klejem CA.
Jeszcze jedno. W kołach, gdzie mamy duże wyoblenia między szprychami należy wypełnić te przestrzenie (umiarkowanie) distalem i okrągłym iglakiem ukształtować. W SM03 na szczęście takiej konieczności nie było bo oryginalnie koła te są dość kanciaste w środku, więc wystarczyło małe "nadlanie" CA i lekki szlif nierówności.”
Koniec cytatu, ten dokładny opis wydaje mi się pomocny, gdyby ktoś chciał przerabiać koła zamiast… kupić w sklepie!
Kolejny problem do rozwiązani to napęd. Początkowo chciałem wykonać go samodzielnie bo w SM 03 jest prosty, zacząłem już rysować i liczyć przełożenia w oparciu o moje zasoby kół zębatych (na zdjęciu).
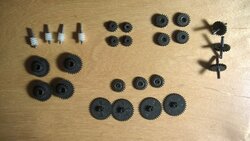
Ale potem puknąłem się w czoło i przypomniałem sobie, że to nie lata 80-te, gdy o gotowych napędach można było pomarzyć (chyba, że ze złomu pikowskiego, którego zawsze pod Halą Targową było sporo) i w internetach znalazłem odpowiedni napęd, z jakiegoś germańskiego tramwaju H0, produkcji PMT. Rozstaw osi pasował idealnie…


…pozostał jednak montaż nowych kół, co nie było proste bo osie dla H0 są krótsze (a koło zębate trzeba było zachować) oraz średnica wału mniejsza niż otwór w kole. Dzięki zastosowaniu tulejki z rurki mosiężnej cel został osiągnięty. Aha, w międzyczasie koła zostały pomalowane a w ramię korby zostały zamontowane czopy wiązarów. Po zmontowaniu wyglądało to już całkiem dobrze, czyż nie?
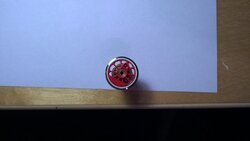
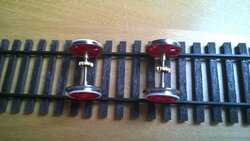
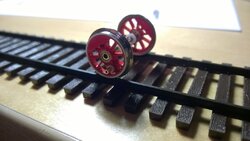
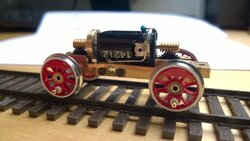
KONIEC CZĘŚCI PIERWSZEJ
-
12
-
1
-
8
- Pokaż wszystkie